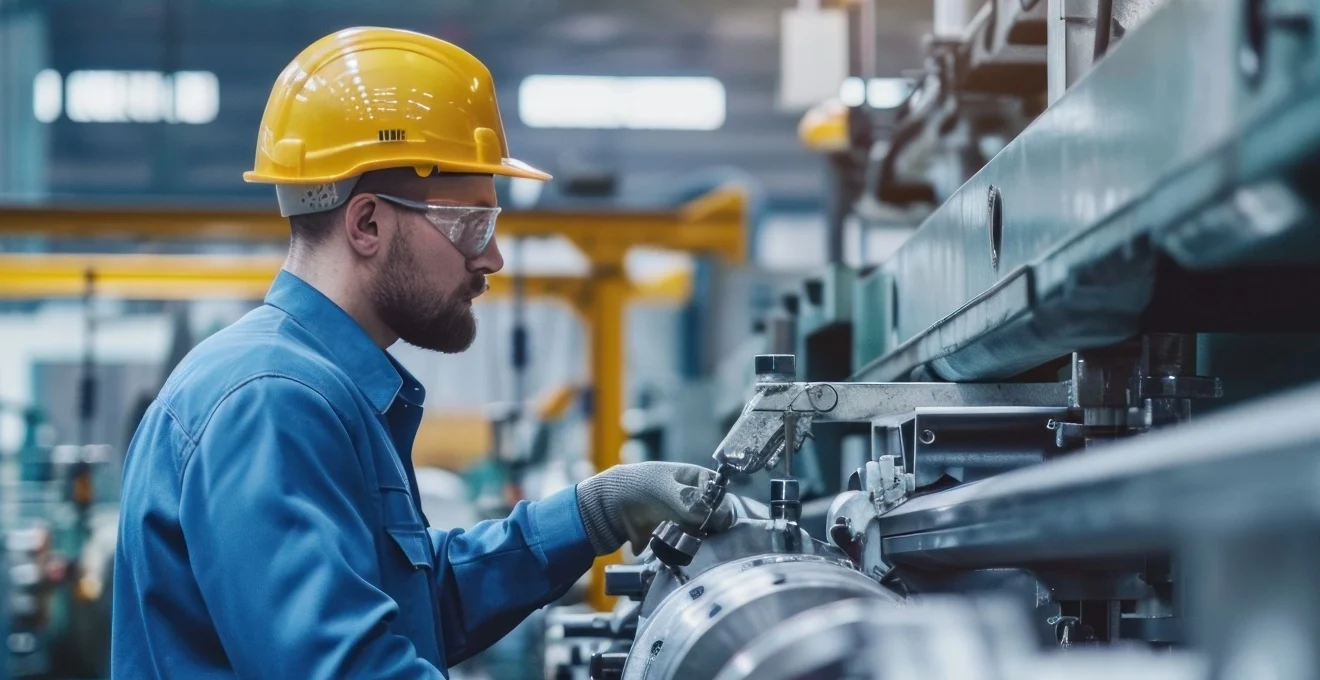
La maintenance industrielle contribue aux performances des entreprises manufacturières. Améliorer ces pratiques permet de maîtriser les coûts d’exploitation et d’assurer une meilleure continuité des opérations et une production de qualité. Avec l’évolution rapide des technologies et la complexité croissante des installations, les entreprises doivent repenser leurs méthodes de maintenance industrielle à Bordeaux ou ailleurs pour rester compétitives.
Maintenance prédictive appuyée par l’intelligence artificielle
L’utilisation de l’intelligence artificielle transforme profondément la manière dont les entreprises abordent la maintenance industrielle. Plutôt que de réagir à des défaillances, il devient possible d’anticiper les incidents avant qu’ils ne surviennent. Cette transition repose sur l’analyse continue de volumes importants de données issues des équipements, permettant de planifier les interventions au moment le plus opportun. Cette anticipation contribue à limiter les arrêts imprévus et à prolonger la durée de fonctionnement des installations.
Surveillance continue grâce aux objets connectés
Les objets connectés rendent possible une observation pointue et permanente de l’état des machines. En installant des capteurs sur les équipements, il est possible de suivre en temps réel des indicateurs comme les vibrations, la température ou la pression. Ces données sont ensuite centralisées pour former une vue d’ensemble de l’environnement de production, accessible à tout moment. Les entreprises à Bordeaux comme ailleurs qui souhaitent faire évoluer leurs pratiques peuvent s’appuyer sur ces outils pour gagner en réactivité.
Prédiction des défaillances avec le machine learning
Les techniques d’apprentissage automatique, via des bibliothèques comme TensorFlow ou scikit-learn, permettent d’exploiter la masse de données générée par les capteurs. Ces algorithmes repèrent des schémas récurrents qui précèdent généralement une panne, rendant possible une intervention préventive bien avant qu’un dysfonctionnement ne se manifeste. Par exemple, un modèle entraîné à partir des incidents passés peut reconnaître des signes faibles annonciateurs de défaillance, plusieurs jours à l’avance.
Simulation dynamique avec des modèles numériques
Les répliques virtuelles d’équipements industriels, alimentées par les données collectées sur le terrain, permettent de simuler le comportement réel des machines. Ces représentations numériques rendent possible l’expérimentation de différents scénarios sans mettre en péril la production. Grâce à ces simulations, les techniciens peuvent émettre diverses hypothèses, ajuster les paramètres d’exploitation et mieux appréhender les causes potentielles de dysfonctionnement.
Diagnostic par analyse vibratoire
L’analyse des vibrations est une méthode reconnue pour détecter des anomalies sur les éléments mécaniques en mouvement. Des techniques telles que la transformée de Fourier rapide ou l’analyse par ondelettes permettent d’identifier très tôt des défauts particuliers, souvent invisibles à l’œil nu. Lorsqu’elle est combinée à des modèles intelligents, cette méthode permet de planifier des interventions ciblées, évitant ainsi que de petits défauts n’évoluent vers des pannes majeures.
Améliorer la maintenance préventive pour renforcer la fiabilité des installations
Même si les méthodes prédictives prennent de plus en plus de place, la maintenance préventive structurée demeure un pilier indispensable pour assurer la continuité des opérations industrielles. Une organisation rigoureuse de ces actions contribue à limiter les interruptions planifiées et à préserver les performances des équipements. À Bordeaux comme ailleurs, le perfectionnement de ces pratiques peut renforcer la compétitivité des sites de production.
Systèmes informatisés pour la gestion des opérations de maintenance
L’utilisation d’outils numériques comme SAP PM ou IBM Maximo permet de structurer l’ensemble des tâches d’entretien des machines. Ces plateformes permettent de planifier les interventions, de suivre leur exécution et de documenter chaque opération, rendant possible un pilotage exact de l’activité. En centralisant les informations, ces systèmes facilitent la coordination entre les équipes et permettent d’appuyer les décisions sur des données vérifiables. Le recours à ce type d’outil est souvent un point de départ pour une organisation plus rigoureuse des activités techniques.
Ordonnancement automatisé des tâches pour un meilleur enchaînement des interventions
Gérer l’agenda des équipes de maintenance suppose de prendre en compte de nombreux paramètres : disponibilité du personnel, degré d’urgence des travaux, contraintes de production ou d’installation. Des outils d’ordonnancement basés sur des modèles mathématiques peuvent ajuster automatiquement les plannings en fonction de ces éléments. Cette démarche contribue à une meilleure utilisation des ressources et permet de réduire les perturbations dues aux arrêts de machines.
Méthodes d’intervention rationalisées grâce à la technique SMED
La méthode SMED, bien que conçue initialement pour améliorer les changements de série en production, peut également s’appliquer à la maintenance. Elle consiste à simplifier et organiser les interventions en amont afin d’en raccourcir la durée. Cela implique une préparation minutieuse des outils et pièces détachées, ainsi qu’une division claire des étapes de travail. En procédant ainsi, il devient possible de diminuer le temps nécessaire aux opérations planifiées et d’accélérer le retour en service des équipements.
Développement des compétences techniques dans un environnement en mutation
Avec l’évolution constante des technologies industrielles, maintenir un niveau élevé de savoir-faire au sein des équipes de maintenance devient un challenge majeur. Pour suivre le rythme des changements, il est indispensable de proposer des parcours d’apprentissage continus, afin que les techniciens restent pleinement opérationnels devant de nouveaux outils, systèmes et méthodes. Une équipe bien préparée, réactive et autonome peut intervenir avec davantage d’efficacité, limitant les erreurs et les délais d’intervention.
Certifications professionnelles pour renforcer l’expertise
Des parcours certifiants tels que CRL (Certified Reliability Leader) ou CMRP (Certified Maintenance & Reliability Professional) permettent aux professionnels du secteur de développer leurs connaissances dans des domaines variés, de la gestion des équipements à l’analyse de performance. Ces programmes encouragent une montée en compétences structurée, en reconnaissant officiellement l’expertise acquise. Valoriser ces démarches peut renforcer l’implication des équipes et donner une nouvelle dimension aux métiers de la maintenance.
Apprentissage immersif avec la réalité augmentée
L’intégration de la réalité augmentée dans les formations permet une démarche plus interactive et concrète. En superposant des instructions ou schémas numériques à l’environnement réel des techniciens, cette technologie rend l’apprentissage plus intuitif et mieux adapté aux situations de terrain. Elle est particulièrement utile pour accompagner les interventions techniques complexes ou peu fréquentes, en facilitant le transfert d’expérience entre opérateurs expérimentés et nouveaux arrivants. Même à distance, il devient possible de guider des interventions avec précision.
Collaboration entre sites pour enrichir les savoir-faire
Favoriser les échanges entre équipes réparties sur différents lieux de production peut améliorer les méthodes de travail. En créant des espaces d’échange réguliers autour de cas concrets, les techniciens peuvent confronter leurs méthodes, partager des astuces techniques et s’entraider devant des problématiques rencontrées sur le terrain. Ces dynamiques collectives stimulent une culture de progrès et renforcent la cohésion des équipes autour de leurs responsabilités opérationnelles.
Réduire les délais d’intervention grâce à une gestion allégée des pièces détachées
Assurer une bonne disponibilité des composants en maîtrisant les coûts de stockage reste un challenge central pour les équipes de maintenance. En s’inspirant des principes d’efficacité issus de la production industrielle, il devient possible de mieux réguler les flux de pièces de rechange et d’éviter les excès ou les ruptures. L’idée est de maintenir un équilibre entre ce qui est nécessaire pour intervenir rapidement et ce qui peut être évité en termes d’immobilisation inutile.
Une des méthodes les plus courantes consiste à classer les pièces selon leur fréquence d’usage ou leur importance pour le bon fonctionnement des équipements, afin d’orienter les efforts de suivi vers les composants les plus sensibles. Par ailleurs, certains systèmes visuels ou numériques peuvent déclencher automatiquement le réapprovisionnement dès qu’un seuil est atteint, réduisant ainsi les oublis ou les retards. Dans certains cas, l’impression de pièces simples via des procédés de fabrication additive permet de répondre rapidement à des besoins ponctuels sans dépendre de délais extérieurs.
Démarche structurée pour mieux anticiper les pannes : méthodes RCM et AMDEC
Pour renforcer la continuité de fonctionnement des installations industrielles, il est indispensable d’analyser en profondeur les risques de défaillance technique. Deux méthodes largement validées peuvent aider à y voir plus clair : la RCM (Maintenance Centrée sur la Fiabilité) et l’AMDEC (étude des modes de défaillance et de leurs conséquences). Toutes deux permettent d’évaluer les points sensibles des équipements et d’adapter les actions de maintenance aux besoins réels du terrain.
La démarche RCM repose sur une analyse pointue de chaque équipement en tenant compte de son usage, de son importance dans le processus de production et des scénarios de défaillance possibles. Elle permet de choisir des actions de maintenance adaptées, ni excessives, ni insuffisantes. De son côté, l’AMDEC examine de manière méthodique les composants d’un système pour déterminer où se trouvent les faiblesses majeures et quelles conséquences peuvent en découler, avec l’objectif d’anticiper les problèmes et de réduire les interventions d’urgence.
Mettre en œuvre ces méthodes permet de concentrer les efforts sur ce qui compte réellement : les équipements exposés aux incidents les plus lourds de conséquences. Cela évite de disperser les ressources sur des éléments peu sensibles et d’apporter un meilleur contrôle sur l’état général du parc industriel. À terme, cela contribue à une meilleure maîtrise des dépenses de maintenance et de renforcer la stabilité du système de production.
Préserver la sécurité dans les opérations de maintenance
Dans les environnements industriels, assurer la sécurité des personnes lors des interventions techniques est un impératif permanent. Trop souvent reléguée au second plan, cette dimension mérite pourtant une attention constante, tant les conséquences d’une négligence peuvent être lourdes. En structurant les pratiques autour de procédures rigoureuses et en sensibilisant les équipes, il devient possible de prévenir les incidents et de maintenir un niveau de vigilance adapté aux réalités du terrain.
Des méthodes comme le nettoyage à ultrasons industriel permettent de réduire l’exposition aux produits agressifs et de garantir des résultats exacts. Ces procédés contribuent à créer un cadre de travail plus sûr, sans compromis sur la qualité de l’entretien.
Se conformer aux référentiels en vigueur
Certaines références internationales apportent un cadre structuré pour organiser les pratiques en lien avec la gestion des équipements techniques. Les lignes directrices proposées par les normes ISO 55000 ou EN 15341 permettent d’encadrer l’ensemble des actions liées au suivi des machines, en combinant paramètres techniques, données économiques et exigences réglementaires. Leur mise en application favorise une gestion maîtrisée et cohérente dans la durée, facilitant aussi les échanges avec les organismes de contrôle ou d’audit.
Sécuriser les interventions sur les équipements sous tension
Lorsqu’un équipement doit être isolé avant maintenance, des protocoles doivent être appliqués pour éviter toute mise en danger. C’est le cas de la méthode dite LOTO (pour verrouillage et consignation), qui impose de neutraliser toutes les sources d’énergie avant l’intervention. Cette pratique, bien établie dans l’industrie, nécessite une organisation stricte, un matériel dédié et une formation claire des intervenants. Des outils numériques peuvent aujourd’hui en simplifier la gestion et renforcer la fiabilité du processus en temps réel.
Travailler en zones sensibles : exigences renforcées
Dans les secteurs où des produits inflammables sont présents, des règles particulières s’imposent. Travailler dans des atmosphères potentiellement explosives nécessite des équipements certifiés, mais aussi des méthodes détaillées et une formation spécialisée. L’organisation des opérations dans ces espaces demande un encadrement minutieux, à la fois pour protéger le personnel et garantir la conformité des installations.
Concilier sécurité, fiabilité et performance
Prendre en compte les règles de sécurité et les obligations réglementaires ne relève pas d’une simple formalité. Ces éléments influencent la qualité des interventions et la stabilité des installations. En développant une culture technique rigoureuse, en renforçant les savoir-faire internes et en intégrant ces exigences aux pratiques courantes, les entreprises peuvent consolider durablement la fiabilité de leur outil de production.